Nylon 6.6 and Nylon 6 are two common types of nylon polymers, which are synthetic materials with a wide range of applications due to their strength, durability, and resistance to wear and tear. Specifically, there are significant differences between Nylon 6.6 and Nylon 6, which are two commonly-chosen options for industrial sewing and filament thread applications.
- Nylon 6 is made from a single monomer type containing six carbon atoms. It has a relatively low melting point, making it easy to process into various forms such as fibers, films, and molded parts. Nylon 6 is often used in carpet fibers, clothing, and packaging materials.
- On the other hand, Nylon 6.6 is made from two different monomers, each containing six carbon atoms. This results in a polymer with a higher melting point, better mechanical properties, and more excellent chemical resistance than Nylon 6. Nylon 6.6 is often used in applications such as automotive parts, electrical components, and industrial fibers.
NYLON 6 | NYLON 6.6 |
Less crystalline | More crystalline |
Lower mold shrinkage | Exhibits greater mold shrinkage |
Lower melting point | Higher melting point |
Lower heat deflection temperature | Higher heat deflection temperature |
Higher water absorption rate | Lower water absorption rate |
Poor chemical resistance to acids | Better chemical resistance to acids |
Withstands high impact and stress and better stand up to hydrocarbons | Better stiffness, tensile modulus, and flexural modulus |
Lustrous surface finish, easy to color | Also easy to color |
Table of Contents
Characteristics of Nylon 6.6 vs Nylon 6
Nylon 6.6 is stronger, more heat-resistant, and more chemically resistant than Nylon 6. However, Nylon 6 is more flexible and easier to process. The choice between the two materials depends on the specific application and required properties.
Nylon 6.6 and Nylon 6 are both types of synthetic polymers with a wide range of applications. Here are some of their characteristics:
Nylon 6.6
Nylon 6.6 is similar to Nylon 6 but not the same. Some industrial fiber processes, like tire cords, use heat to incorporate the fiber into the end product. Nylon 6.6 withstands these processes and continues to provide reliable strength well afterward. Nylon 6, by contrast, degrades or forces a change in the processes, reducing productivity.
Nylon 6.6 offers low creep, good stretch recovery, and higher abrasion resistance than Nylon 6 and most other materials in the marketplace. Its abrasion and heat resistance are the defining properties that make it a superior choice for industrial applications.
The Nylon 6.6 are 33% more abrasion resistant than Nylon 6 fibers, withstanding over 60,000 cycles over Nylon 6’s 40,000 cycles. In hard-wearing industrial fiber applications, this means much more reliable long-term performance.
- Made from two different monomers, each containing six carbon atoms
- It has a higher melting point than Nylon 6
- Greater chemical resistance than Nylon 6
- Higher tensile strength than Nylon 6
- More heat-resistant than Nylon 6
- Can withstand higher temperatures without breaking down
- Used in automotive parts, electrical components, and industrial fibers
Nylon 6
Nylon 6 has the core characteristics of any member of the nylon family, including its hardness, stiffness, and toughness. It has good mechanical dampening and insulation qualities.
It slides with minimal abrasion, resists fatigue, and is very wear-resistant over time. As an added benefit, it has good machinability and can be worked into its final form fairly easily. It also has a lustrous finish. Here are some of Nylon 6 characteristics:
- Made from a single type of monomer, which contains six carbon atoms
- Has a relatively low melting point
- More flexible than Nylon 6.6
- Easier to process than Nylon 6.6
- Used in carpet fibers, clothing, and packaging materials
Applications
Both Nylon 6.6 and Nylon 6 are useful in different applications due to their properties. Nylon 6.6 is generally used in industrial and high-performance applications that require strength, heat, and chemical resistance. Nylon 6, on the other hand, is used in textiles, consumer goods, and packaging due to its ease of processing and flexibility. Both Nylon 6.6 and Nylon 6 are widely used in different industrial and commercial applications due to their desirable properties. Here are some common uses of each:
Applications of Nylon 6.6
Nylon 6.6 has several primary uses, including micro denier vs. heavy denier vs. high-tech. In its micro-denier form, it is mostly used in apparel. It offers great toughness and wears resistance for high-performance sports gear and industrial workwear.
In its heavy denier form, it is used in tires and industrial products. In its high-tech form, you’ll find it in automotive airbags, parachutes, carpets, and other uses where extreme performance, durability, and reliability are of the utmost importance.
- Automotive parts: such as engine components, clips, and fasteners
- Electrical components: wiring, connectors, and housings
- Industrial fibers: ropes, webbings, and belts
- Textiles: High-performance clothing, sportswear, and backpacks
- Consumer goods: luggage, camping gear, and outdoor furniture
Applications of Nylon 6
The major use of Nylon 6 is in industrial yarn. It is found in cords, heavy-duty fabric, toothbrush fibers, and many other products that rely on tough industrial nylon for a blend of strength and flexibility.
Nylon 6 is also found in fabrics with a specific type of desirable fashion sheens like hosiery, chiffon, and organza. This is due to the lustrous surface finish that is unique to Nylon 6.
- Carpet fibers: Due to abrasion and stain-resistant have versatility in various colors.
- Clothing: Used in stockings, lingerie, and sportswear
- Packaging materials: such as films, monofilaments, and nets
Nylon 6.6 and nylon 6 sewing thread
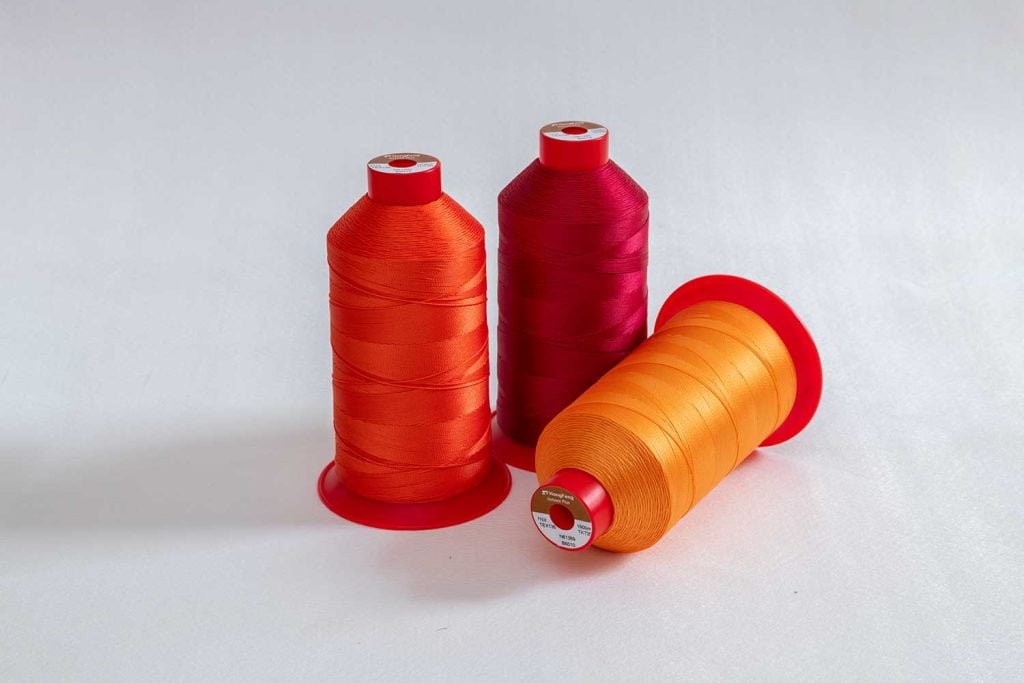
Nylon 6.6 and nylon 6 are commonly used to make filament sewing threads due to their strength, durability, and resistance to wear and tear.
Nylon 6.6 threads are made from a polymer with a higher melting point and greater chemical resistance than Nylon 6. This makes them more suitable for applications where the thread may be exposed to heat or chemicals, such as sewing automotive or upholstery fabrics, outdoor gear, and industrial textiles.
Nylon 6 sewing thread is a type of synthetic thread made from the polymer nylon 6. It is known for its strength, durability, and toughness, which make it an excellent option for sewing various types of fabrics.
Both Nylon 6.6 and Nylon 6 threads offer good elasticity, strength, and abrasion resistance, making them suitable for sewing a variety of materials such as cotton, wool, and synthetics. The choice between the two types of thread depends on the application, the materials being sewn, and the desired properties of the finished product.
Top 7 features of nylon 6 sewing thread
- Excellent flexibility: Nylon 6 sewing threads have an extremely high degree of flexibility, which makes them ideal for sewing items that require a lot of movement or stretching, such as sportswear or dancewear.
- High moisture absorbency: Nylon 6 sewing threads can absorb moisture more readily than other types of synthetic threads, which can make them more comfortable to wear in warm or humid environments.
- Resistance to abrasion: Nylon 6 sewing threads have excellent resistance to wear and tear, making them particularly suitable for sewing materials that are prone to abrasion or friction, such as canvas and denim.
- High tensile strength: Nylon 6 sewing threads offer a high degree of tensile strength, which allows them to hold up against significant amounts of tension without breaking.
- Ability to withstand high temperatures: Nylon 6 sewing threads can withstand high temperatures for extended periods, making them well-suited for industrial sewing applications.
- Easy to dye: Nylon 6 thread can be dyed to a wide variety of colors, making it suitable for use in a range of sewing projects.
- Good elasticity: Nylon 6 thread can stretch without losing its shape or breaking, which can be beneficial when sewing items that need to move or stretch with the body.
Top 5 features of nylon 6.6 sewing thread
- Excellent tensile strength: Nylon 6.6 sewing threads are highly resistant to breakage and can withstand a great amount of stress, making them ideal for use with heavy-duty fabrics and in high-stress environments.
- Resistance to abrasion and wear: Nylon 6.6 threads’ excellent resistance to abrasion and wear makes them suitable for use in textiles and fabrics that receive a lot of wear and tear, such as outdoor gear, automotive textiles, and industrial textiles.
- Resistance to chemicals: Nylon 6.6 threads are highly resistant to chemicals, making them suitable for use in chemical environments such as laboratories or manufacturing facilities.
- Good UV resistance: Nylon 6.6 threads offer good resistance to exposure to ultraviolet light, which can cause other types of synthetic threads to break down over time.
- Ability to withstand high temperatures: Nylon 6.6 threads can withstand high temperatures without breaking down, making them suitable for applications involving heat or high levels of friction.
Works Cited: The Difference Between Nylon 6.6 and Nylon 6