Villtex®
Poly Poly Core Spun Thread
Core Spun Polyester Thread
Hongfeng Villtex® Poly/Poly Core Spun Thread can be used in a wide range of fabrics from silks to high-performance materials. With the advantage of excellent seam strength and superior low-friction lubrication, Hongfeng Villtex® can enhance the appearance of sewn products and significantly improve the productivity and performance of the sewing production line.
The standard for color fastness of core spun polyester thread
International standard | Name | Degree of staining |
ISO 105 C10 | Wash Fastness | Grade 4 |
ISO 105 X12 | Rub Fastness | Grade 4 |
Colorfastness test of Villtex® Poly Poly Core Spun Thread
International standard | Soap solution | Temperature | Time | Degree of staining |
ISO 105 C10 | 5g/L | 60℃+/-2℃ | 30Min | Grade 4 |
Features of Villtex® Core Spun Polyester Thread
- Excellent Strength
- Excellent Seam Strength &Appearance
- High-Level Color Fastness
- OEKO-TEX Standard 100
- Minimise Seam Puckering
- Chemical Resistance
Further reading

What is Core Spun Polyester Sewing Thread
Corespun threads sometimes referred “core” “polypore” or “cotton core”, are made by wrapping a staple polyester or cotton wrapper around a continuous filament bundle of polyester fibers during spinning and then plying these yarns into a sewing thread. The continuous filament polyester core makes up approximately 60% of the thread construction.
The strength depends on the core thread, and the wear resistance and heat resistance depend on the outer yarn. It is mainly used for high-speed and firm garment sewing.
Core Spun Polyester Thread is used where high tensile strength is needed using automatic sewing machines and color fastness is a requirement. Its strength means it is ideal for minimizing sewing problems as smaller thread sizes can be used.
Application of Core Spun Polyester Sewing Thread
The core-spun polyester thread gives the look of a cotton thread but provides superior strength and durability.
Spun Polyester thread is ideal for any manufacturing need from apparel, auto upholstery, and undergarments to high-tech needs such as medical devices, shoes, and more.
- Buttonhole stitching, ultra-thin overlock, blind stitch sewing
- Elasticity, high-grade trimming, jeans, blazers
- Fine blouses that are susceptible to seam puckering, denim products that will be stone-washed or sandblasted
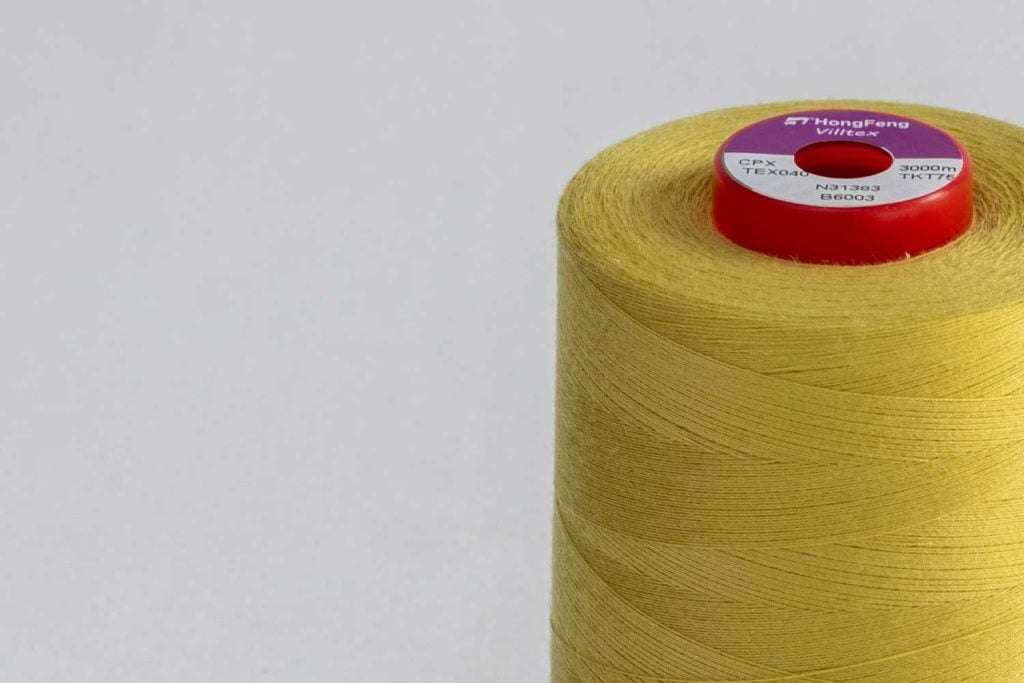

Advantages of Core Spun Polyester Sewing Thread
- Higher strength per size (higher tenacity)
- Greater uniformity in size, strength, and other physical characteristics•
- A higher initial modulus or resistance to stretching contributes to better loop formation and reduced seam puckering.
- Better ply security – fewer unravel-type thread breaks
- Superior abrasion resistance & durability
Core Spun Polyester Thread VS Filament Thread
- A softer “hand” or feel than a 100% continuous filament threads
- A matte finish stitch appearance similar to a spun thread construction
- Superior frictional characteristics compared to continuous filament threads
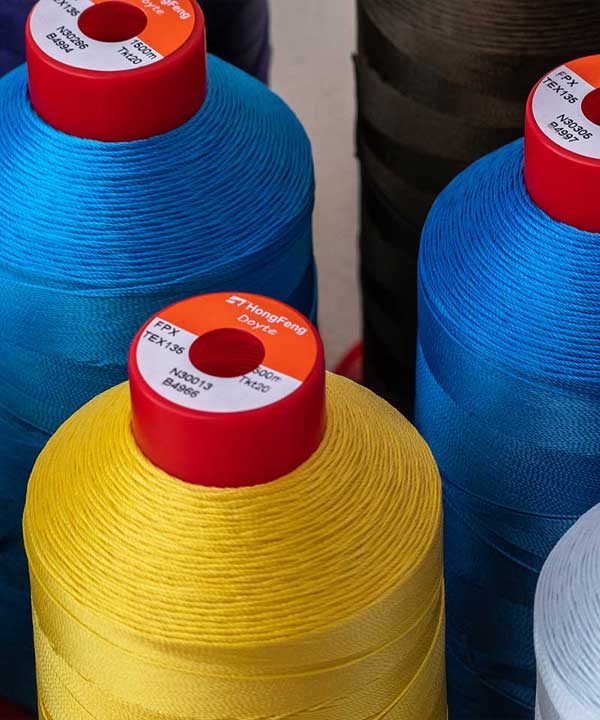
Poly/Poly VS Polyester Cotton Core Spun Thread
The Poly wrapper contributes to :
- Superior color fastness, chemical, and abrasion resistance
- Higher strength than cotton-wrapped core spun threads
- Superior “union dyeing” because of the one-step dyeing process
The Cotton wrapper contributes to :
- Superior needle heat resistance
- A “wash-down” stitch appearance
What are the benefits of using core-spun sewing thread on denim?
- 40 to 50% stronger than spun polyester threads the same size
- Superior sewability on both manual and automatic machines with minimum interruptions – fewer restitched seams.
- Helps to Minimize Open-Seams and Seam Failure
- Allows the use of smaller diameter thread to minimize Seam Puckering or Needle cutting
- Helps to minimize broken and cut stitches after finishing.
Cost Vs Performance
Core-spun polyester threads are more expensive than spun polyester threads.
The usage of these yarns can increase the cost of production. However, using spun polyester yarns can increase the possibility of broken stitches and rejected garments or needing repairs.
A & E mentions that certain manufacturers have tried to use both Core Spun and Spun Poly to achieve a balance between costs and performance.
Since overedge seams consume the most thread, they will use spun polyester on these operations while continuing to use core-spun threads on all topstitching and stress seam operations.