Table of Contents
Faults 1#: The first needle breaks, and the end of the broken thread is cut
- Analysis: The machine needle is installed reversely or the machine needle is not fully installed, resulting in the machine needle being too low. The sewing material is too hard, the needle is too thin or the pressure of the presser foot is too high.
- Solution: Check the installation of the machine needle and whether the screw connecting the needle bar is loose. Replace the needle or adjust the presser foot pressure.
Faults 2#: The suture is crimped at both ends of the severed end with short whiskers
- Analysis: The clamping thread is too tight or the suture is twisted during sewing. The suture is squeezed into the guide groove of the shuttle bed by the shuttle. The sutures are brittle and easy to knot, the quality is poor, and there are burrs on the thread passing parts.
- Solution: Change the pressure of the wire clip and check the wire passing line to eliminate the winding. Check the shuttle for wear and replace if necessary. Sand the threaded area and replace the stitches.
Faults 3#: The thread accumulation in the lower part of the sewing material is heavy, the stitch length cannot be formed and the thread is broken, and the broken thread end is in a horsetail shape
- Analysis: The cloth feed dog is too low, and the sewing material is broken because of too many accumulated lines before the sewing material stops. The feeding cloth and the thread are out of step and broken. The presser foot and the needle are loose, hindering the movement of the sewing material.
- Solution: Raise the feed dog, adjust the positioning angle of the feed cam, tighten the presser foot and the needle screw.
Faults 4#: The thread breaks suddenly during sewing, and the upper thread has curved waves
- Analysis: The position of the shuttle bed is not installed and the upper thread is rolled into the shuttle bed. The bobbin case is locked at the end or suddenly shifted during sewing. The quality of the shuttle is poor. The bobbin spring is too long or the heart sleeve is elliptical.
- Solution: readjust the position of the shuttle bed, reinstall the shuttle, and replace the shuttle with the center sleeve.
Faults 5#: The bottom thread breaks suddenly during sewing
- Analysis: The bobbin sleeve is unqualified, and the inner diameter is elliptical, causing the bobbin to fail to rotate. The bobbin spring screw is over-tightened so that the pressure on the shuttle is too small. The bobbin is overwound or too loose and tangled. The bottom thread is rotten and brittle, with knots, so that the bottom heart cannot pass through the bobbin spring.
- Solution: Replace the bobbin case, loosen the bobbin spring screw, rewind the bobbin thread, and replace the bobbin thread.
Read More: Filament Sewing Thread
8 Other Causes of a Sewing Machine Broken Thread
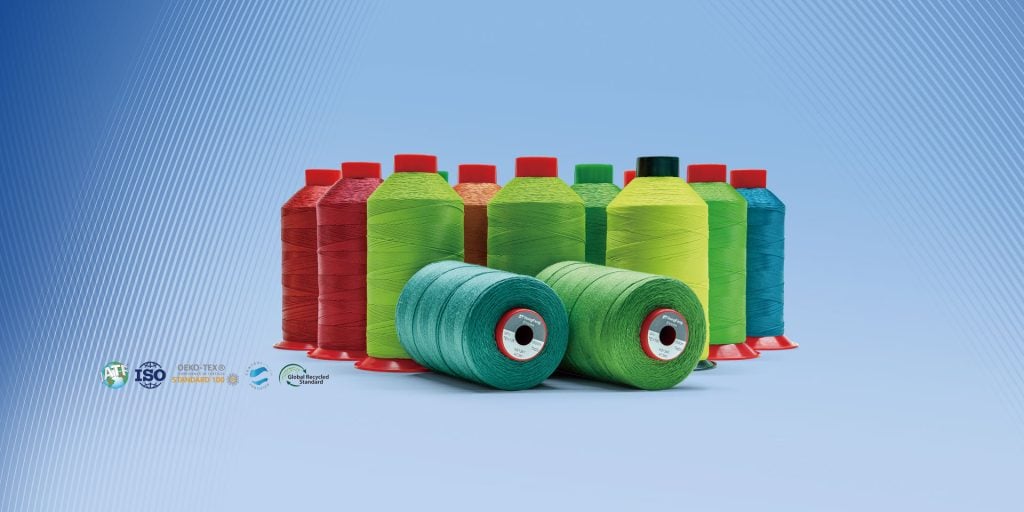
- The threading method is incorrect. Re-thread according to the “threading diagram”.
- The needle is installed incorrectly. Reinstall the needle so that the needle slot faces the operator
- The eye and groove of the needle are not smooth Replace the needle with a new one.
- The suture tension is too high. Adjust the suture tension properly.
- The quality of the suture is too poor, use a better suture
- If the suture is thicker than the needle eye, use a moderate suture or needle
- There are burrs or scratches in the thread holes such as sewing machine needle, looper, needle plate, presser tongue, thread hole, etc. Use oil stone or fine sandpaper to re-polish, or replace the scratched parts.
- Improper coordination of machine needles, loopers, and stretching needles Readjust according to the matching standards of machine needles, loopers, and stretching needles.
Read More: Thread for Sewing Machine