Table of Contents
Reason Type 1#: Broken needle for sewing thick materials
- Analysis: The needle is too thin or bent, the thickness of the sewing material is uneven, and the needle bar moves too much.
- Treatment method: replace the thick needle with a new one, adapt to slow down the sewing speed and help feed the material by hand, and replace the needle bar or needle bar cover with a new one.
Reason Type 2#: Short stitches keep needles, long stitches break
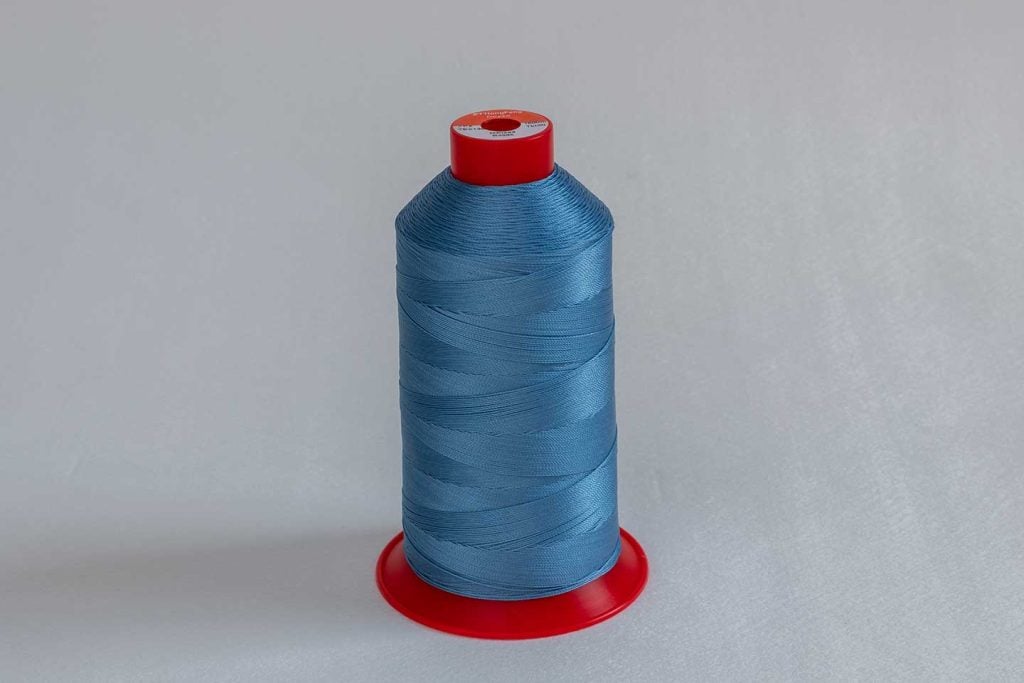


- Analysis: The movement of the cloth feed dog is lagging, the cloth feed dog is unqualified, and the needle breaks when the needle hits the rear end of the cloth feed dog.
- Treatment method: Adjust the positioning of the cloth feed cam, shorten the needle distance appropriately or replace the cloth feed dog with a new one.
Reason Type 3#: The needle is broken under the needle plate
- Analysis: The position of the needle is low, the needle hits the shuttle, the shuttle bed is not installed properly, the tip of the shuttle hits the needle, the gap between the shuttle support and the needle end is too small or too large, the shuttle touches the needle or loses the protection Needle action.
- Treatment method: adjust the position of the needle bar or machine needle, reinstall the shuttle, and adjust the end clearance between the shuttle support and the needle.
Reason Type 4#: The needle breaks on the needle plate
- Analysis: The sewing material is pulled too hard by hand, causing the needle to bend, the presser foot screw to loosen, causing the presser foot to tilt and hit the machine needle, the displacement of the cloth feeding cam, causing the sewing material to break the machine needle, and the hard object in the sewing material to break the machine needle.
- Treatment method: strengthen the operation practice, adjust the presser foot to tighten the screw, and adjust the position of the feed cam screw.
Read More: Filament Sewing Thread
Reason Type 5#: Other 8 reasons
- The pressure of the presser foot is too low, and the needle is broken due to poor cloth feeding. Properly increase the pressure of the presser foot to make the cloth feeding normal.
- The collision between the looper and the straight needle Adjust the matching position of the looper and the straight needle according to the standard.
- The collision between the stretching needle and the straight machine needle Adjust the matching position of the stretching needle and straight machine needle according to the standard.
- Improper cooperation between the straight needle and the needle guard bar. Adjust the match between the machine needle and the needle guard bar according to the standard.
- The tip of the looper is round and bald Replace the looper with a new one.
- The needle bar and needle bar sleeve are worn too much, which makes the needle bar and needle bar sleeve lose. Replace the needle bar and needle bar sleeve.
- The needle holes on the needle plate are too small. Replace the needle plate with large needle holes or replace the needles with smaller ones.
- The parts are loose. Check the fit and wear of the parts of the thread hook mechanism, adjust the matching size according to the standard, and replace the parts with serious wear.
Read More: Thread for Sewing Machine